The 4 Key Factors Behind Superior Paper Cores
When it comes to everyday items like paper towel rolls, carpeting, and plastic wrap, we often overlook the importance of the paper core that supports these products. However, for those in the business of manufacturing paper cores, the process and quality are of paramount importance. Subpar cores can lead to business losses and damage your clients' products. Obviously this is something we in the tube and core business strive to avoid, so let’s look at the top 4 aspects that play a crucial roll in making superior paper cores.
1. Precision Matters

While paper cores may appear to be a minor component in product packaging, they have a significant impact on overall packaging quality and product sustainability. If you've ever encountered toilet paper rolls with flimsy, substandard cores, you know how they struggle to maintain their shape and usability. Such products not only get rejected but also tarnish a brand's reputation. Paper cores come in various widths and must be customized in length as per orders. Even the slightest deviation from accurate dimensions can result in damaged products during packaging and transit, or at the very least, frayed or unsightly edges from cores cut too long. Its imperative that the paper core provider collaborate closely with your manufacturing team to guarantee that your paper cores adhere to precise specifications.
2. Quality In, Quality Out: Better Paper Makes a Better Core
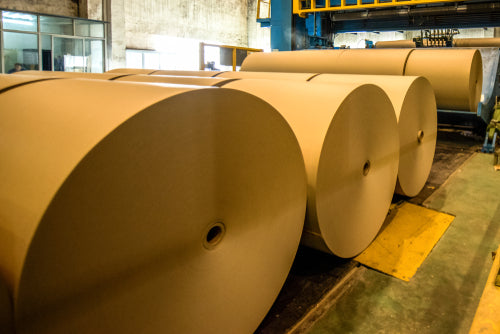
The quality of paper cores hinges on the type of paper used in their production. Just because we at Erdie use recycled paper, doesn’t meant that we can afford to let quality slide. Not all recycled pulp is of the same standard. Fibers can break down over time, so to make a sturdy paper core you need to source pulp with robust fibers that can maintain the core's shape over an extended period. Attempting to fashion cores from paper with low fiber quality will result in cores lacking the strength and stability required to support products like paper rolls, kitchen towels, foil, and wraps.
3. Quality Adhesives: Ensuring a Solid Bond
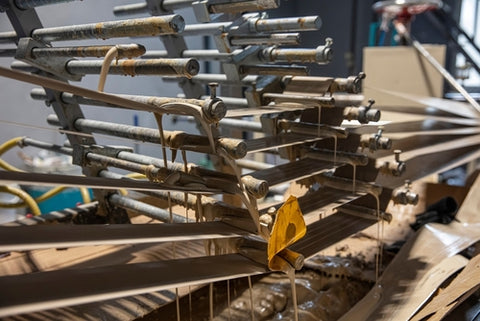
In addition to using high-quality paper, it's crucial for the paper core to incorporate a top-notch adhesive. This adhesive forms a robust bond between each layer of paper, ensuring a sturdy core. Some adhesives are designed to make the paper cores waterproof, while others provide exceptional stability, allowing the core to support substantial product weights. The importance of the the adhesive is paramount and unique to the paper core company and their unique process. Erdie, like others in the industry, create their own in-house proprietary glue to ensure that the end product performs to exact expectations.
4. Test, Test and Test Some More
Before a new product is brought to the table, gaining an understanding of how it will perform in the real world is critical. With every step in the manufacturing process methodically calculated, the last step is to torture test the product to know for certain if it will work with the client’s product. Different paper core manufacturers utilize different testing methods. At Erdie, we use a radial crush machine. This asset has enabled us to meticulously test numerous paperboards and adhesives, helping us enhance our tube and core designs to meet the demands of incredibly demanding industries like Film and Flexible Packaging.
Elevating the Role of Paper Cores
While the significance of paper cores in the packaging world may be underestimated, meticulous production practices can significantly enhance their quality, ultimately leading to improved profitability. High-quality paper cores not only ensure the structural integrity of the packaged products. By focusing on accurate specifications, using premium components, and conducting quality testing, you can become a trusted partner in the world of flexible packaging. In doing so, you'll contribute to the success of your clients and the overall quality of the products that reach consumers' homes on a daily basis.